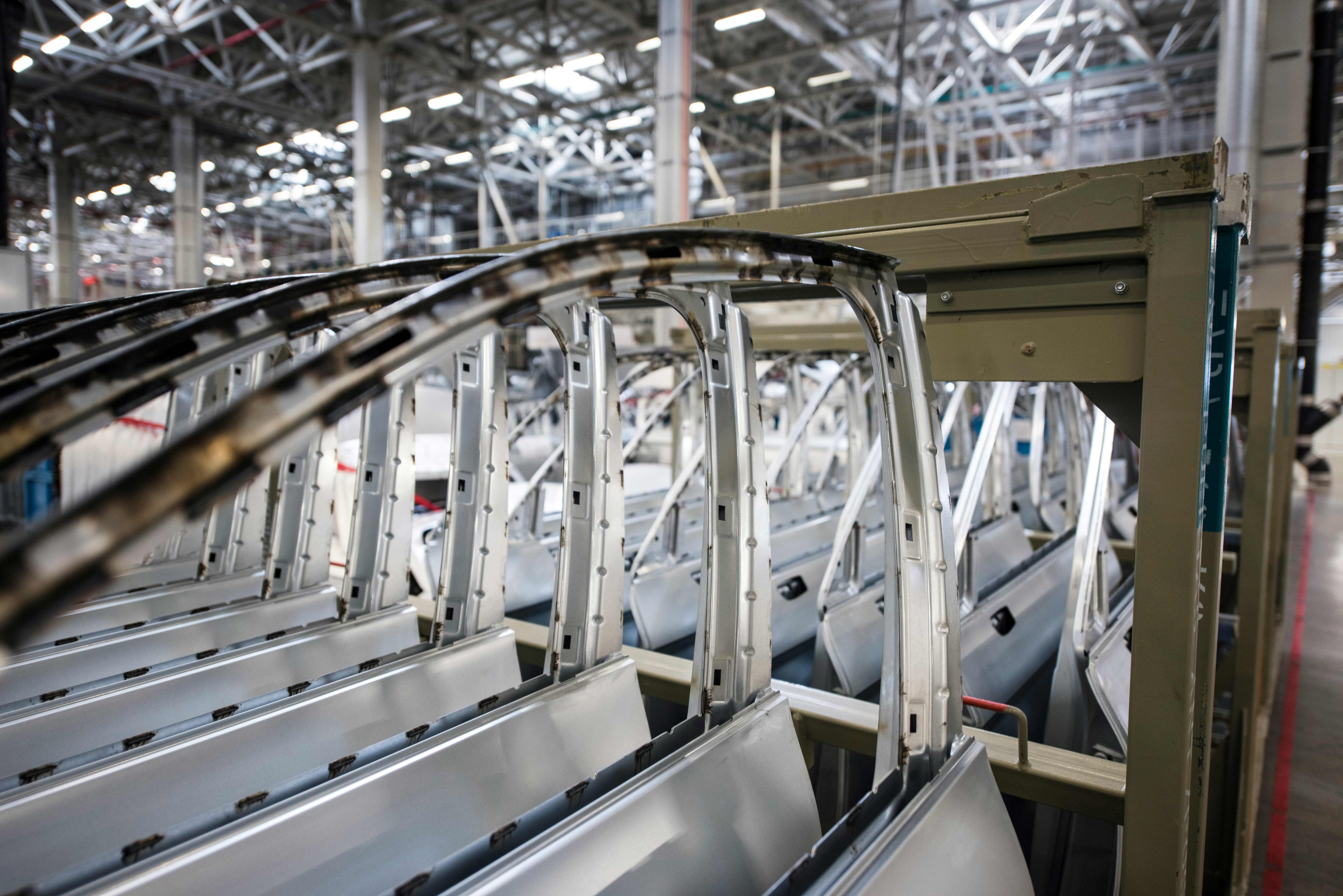
Judging whether an O.E.E. score is now good or of a low level depends on many factors, for example which sector as well as which calculation is behind it. After all, the O.E.E. is partly influenced by the sales of products produced on a machine.
If we abstract from the above factors, it is safe to say that the following segments are used globally as O.E.E.
- 85% and above: Achieving this level places a company in the regions of global excellence (world class manufacturing), a pinnacle achieved by only a handful of manufacturers worldwide.
- 60% - 85%: Reaching this range represents a commendable target range for manufacturers, an example of a balance between operational efficiency and room for incremental improvements.
- 40% - 60%: Within this range, a reasonable O.E.E. score emerges, characterising a significant segment of manufacturers who are actively refining their production processes.
- 40% or lower: Scores in this lower quadrant indicate urgent corrective action. A resolute strategy should be deployed to improve O.E.E. metrics to catalyse optimisation of operational performance.
What is the role of a Stanwick consultant in O.E.E. improvements?
From Stanwick, we have 3 possible roles that we include in operational excellence processes where we improve Overall Equipment Effectiveness (O.E.E.):
- Stanwick trainer
- Stanwick consultant
- Stanwick interim project manager
Learn more about the 3 roles: https://www.stanwick.be/en/about-stanwick
What are the Stanwick cases in Operational Excellence trajectories?
From Stanwick, we have supported several O.E.E. transformation projects in numerous sectors (chemical, pharmaceutical, petrochemical, food, construction industry).
Learn more about our cases: https://www.stanwick.be/en/cases
Feel free to contact us for more info.
Jeroen Van den Hove
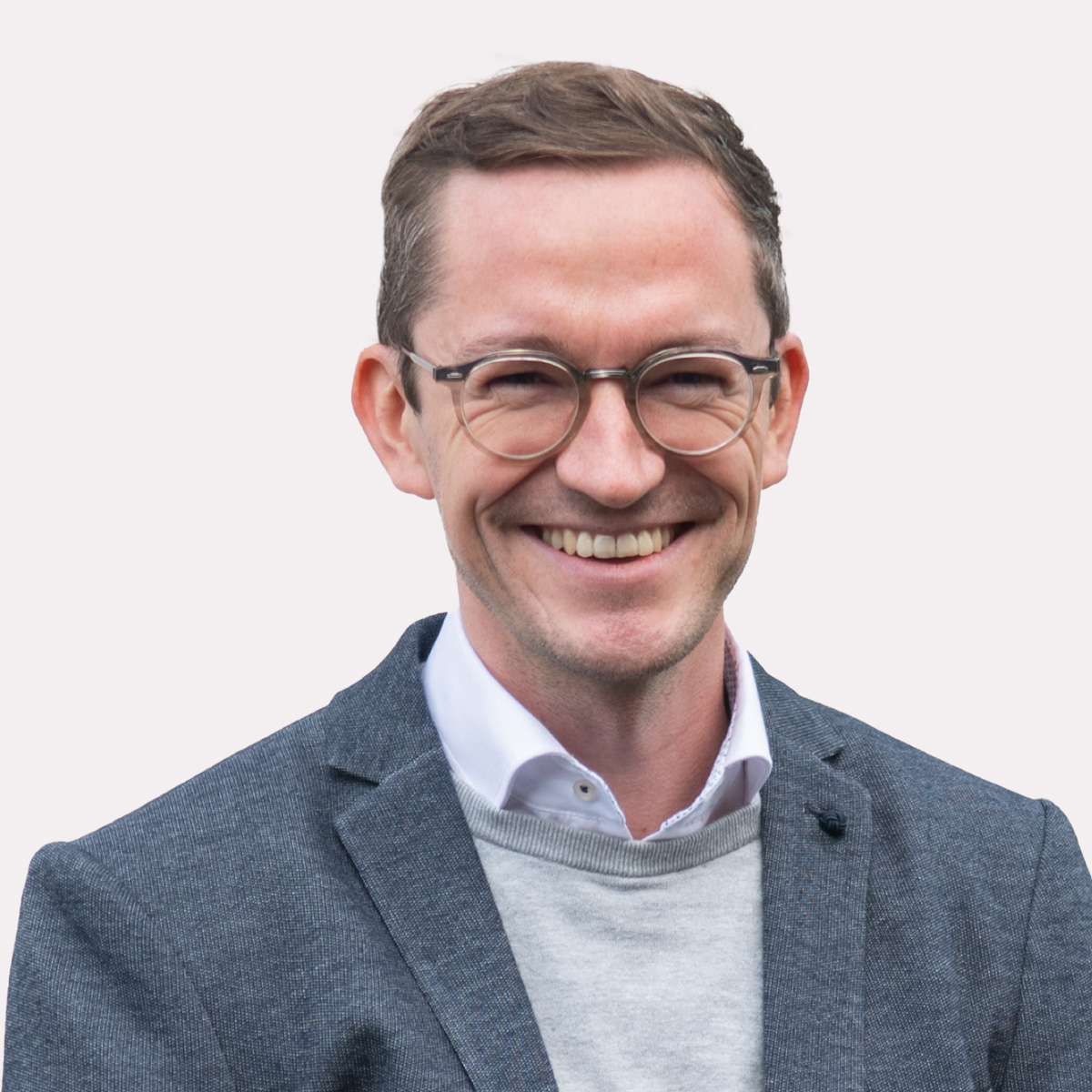