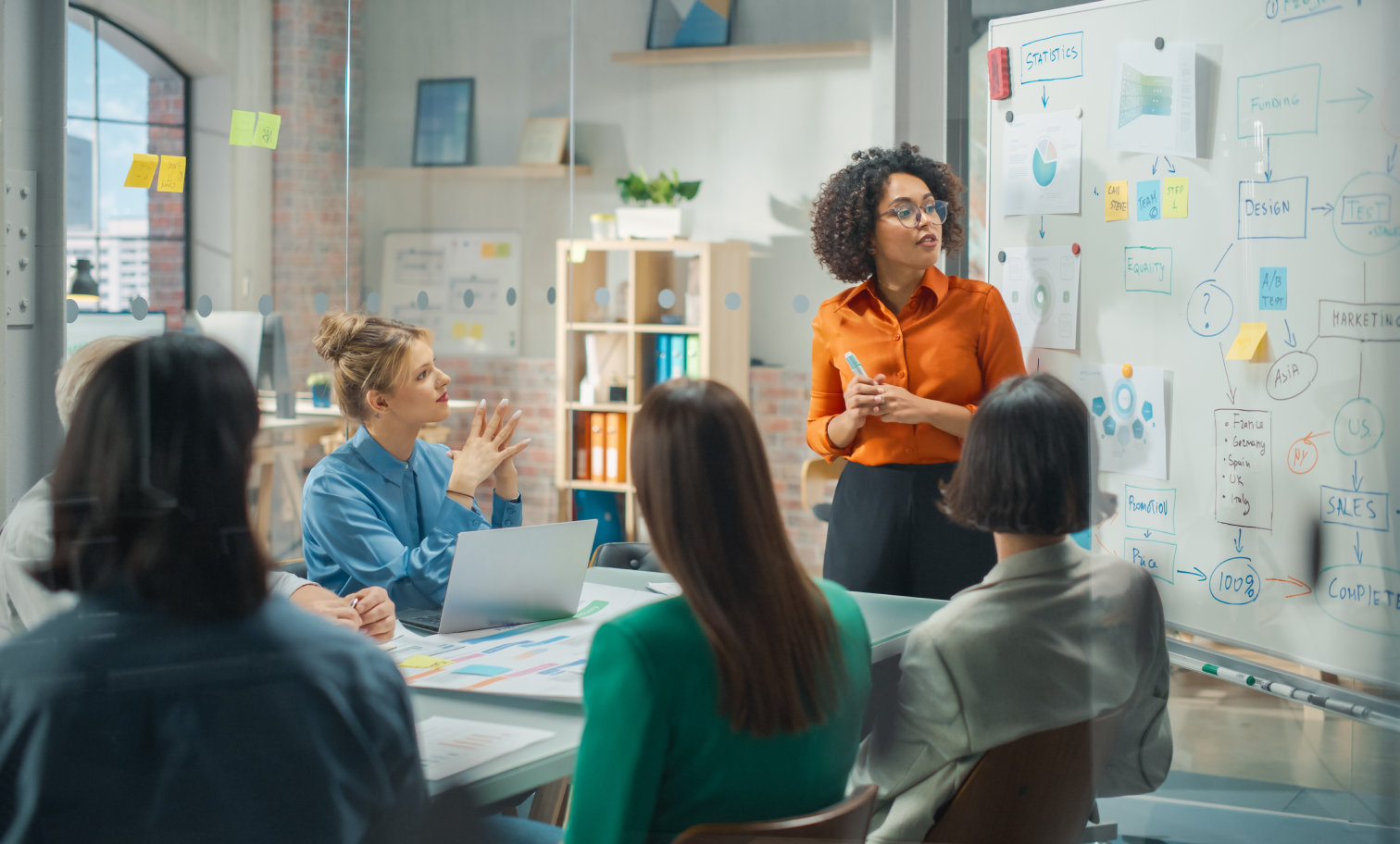
Lean
'Lean' strives for high quality, low costs, reliable and short delivery times, with a minimum of resources. The Lean system consists of a large number of smart technologies & applies to both production, administration (Lean Office), and supply chain (Lean Supply Chain, Lean Warehouse).
The 5 core principles of Lean are:
- Define 'value' from the customer perspective: What is value for the customer? What does the customer wants to pay for?
- Identify all necessary steps to design, order & produce the product across the entire 'value stream (via 'Value Stream Mapping' or VSM)
- Implement 'Flow': produce the right volume according to the customer demand, with the right quality within the agreed delivery time by eliminating non-value adding activities.
- Only do what is requested by the customer, work according to the Pull principle.
- Strive for perfection by continuously eliminating losses. Do not work harder, but smarter!
The Lean system consists of a large number of smart technologies. The key is to use them in a targeted way, so cherry-picking is not enough. See below a selection of the 'Lean building blocks' that we use in Stanwick in production, office, warehouse, supply chain, ...:
- Systematic planning: One-piece flow - FIFO - Supermarket - Kanban - One Point Scheduling - Planning wheel - Line balancing – Load levelling (Heijunka) – Mixed Modelling – Value Stream Mapping
- Systematic working: Single Minute Exchange or Dies (SMED) - Standard work - Poka Yoke - 5S - Visual Management – Andon – Cell Layout - Kaizen – Go to gemba
- Systematic design: 3P (Production Preparation Process)