Operational Excellence
In the fast-changing world of manufacturing, achieving operational excellence is no longer an option, but a necessity.
What is an Operational Excellence organisation? “An organisation that consistently delivers products and/or services meeting customer expectations for quality, delivery performance, and cost, while remaining profitable in both the short and long term, maintaining a strong commitment to safety and environmental responsibility, and achieving a good balance between what is demanded of and offered to its personnel, can be considered excellent.”
Evolving towards Operational Excellence can be a bumpy road
Throughout our years of experience across numerous companies and cultures, we have occasionally encountered organisations that excel in some of these areas, but rarely all at once. Unfortunately, we have often observed companies that spend too much time looking back, unaware that a nostalgic pride for past achievements can stand in the way of real innovation and excellence. Even more concerning, we have sometimes witnessed signs of institutionalised immobilism, where processes are so rigidly locked up in their own spiderweb of rules that even the most courageous employees cannot drive change towards excellence.
Leadership in problem solving & process improvement
To achieve this level of Operational Excellence, these organizations invest continuously in quality improvements, and if issues arise, they’re ready with thorough root-cause analysis and a problem-solving mindset. Leaders in these organisations lead by example, act as mentors and coaches, and keep their focus on the future, rather than getting caught up in the past. An Operational Excellence organisation strives for always having an ideal batch:
"An ideal batch is produced to meet the customer’s required standards, within the expected timeframe, with no workarounds, no managerial interference, no quality issues, and as cost-effectively as possible."
Organisational structure and managing value-added work
To achieve this level of excellence, it’s essential for organisations to also invest in their structure. When we look at organisations today, we often notice they are top-heavy. The balance between employees delivering value-added work and those overseeing the organisation’s activities is frequently misaligned. We think it is crucial to strive for efficient support departments and connect all departments through a clear governance model. In our opinion, an excellent organisation should strive for the Pareto principle, where at least 80% of the workforce is engaged in value-added work, delivering products or services according to the operational excellence definition, while 20% or less is involved in governance.
High performing organisations based on capability building and policy deployment
This governing portion of the organisation ideally acts as an enabler for the value-added work. They lead by example, offer training, provide help and support, assist in achieving set goals, and foster a high-performing environment with clearly defined and shared roles and responsibilities.
Additionally, they maintain a forward-looking perspective, asking: What are the organisation’s next goals? What is happening in the broader world, especially in our field and industry? Based on these insights, they set and communicate new short- and long-term goals to the entire organisation.
Want to know more? Reach out.
At Stanwick, we take a tailored approach to achieving your business goals. Want to know more about how we can support your organisation? Contact us for more information.
Operational Excellence - Cases
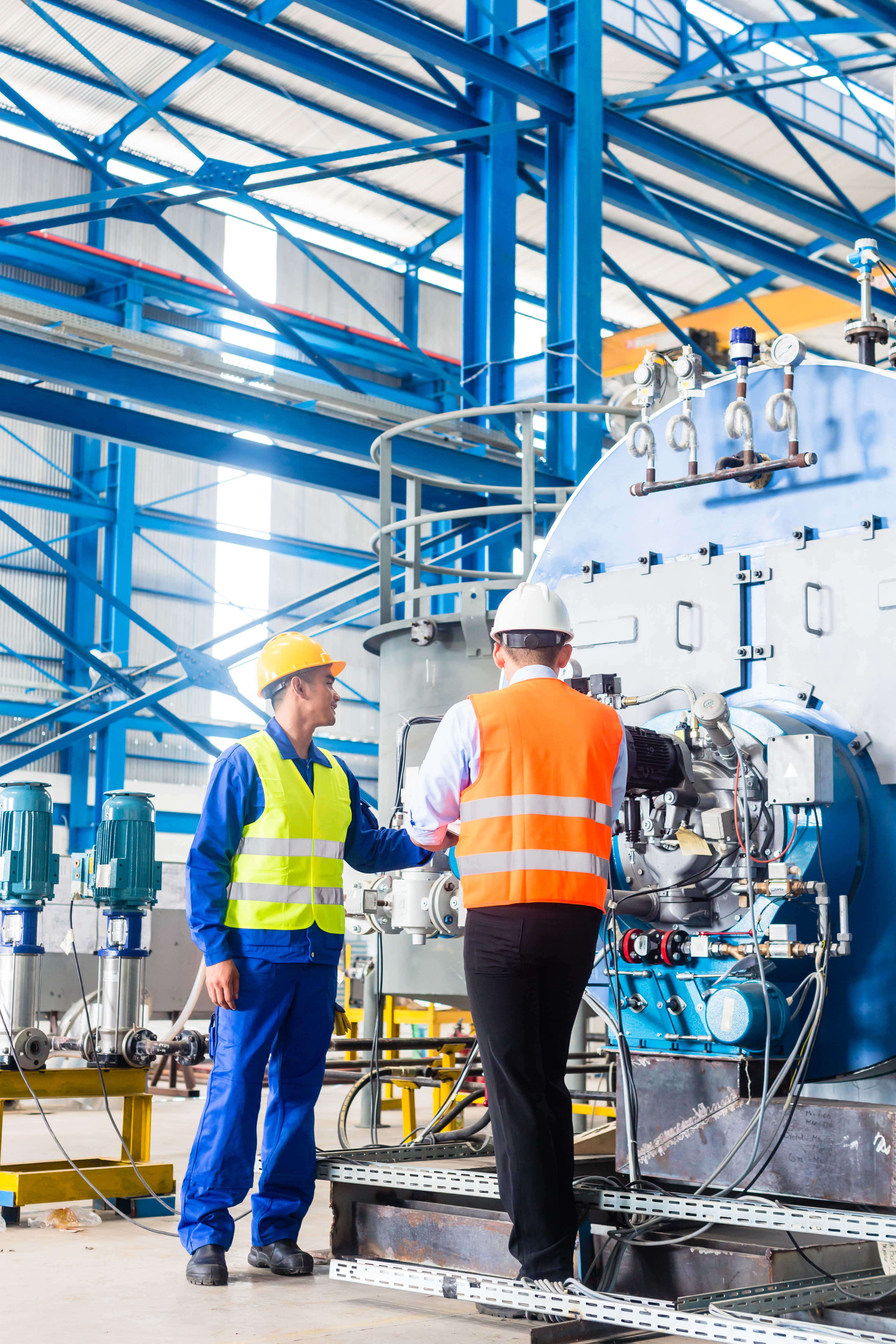
How does Stanwick help your organisation?
We use Operational Excellence as a methodology to professionalise the way processes, people & teams work within your organisation:
- We carry out an operational excellence assessment, establishing an implementation plan with all partners involved and creating the necessary commitment.
- We define 1 unified operational excellence approach and language, an approach based on customer reality by thinking in value streams. A pragmatic approach that is usable for all supply chain processes and teams in the organisation and builds maximally on what is already there.
- We set up a training and capability building programme to familiarise your employees with the operational excellence approach and language.
- We pay attention to creating the framework conditions and align business processes with the operations management and organisational design approach and link them to the business strategy.
- We install an effective tiered accountability approach (performance management) that manages daily performance with result-oriented KPIs.
- We can switch between long-term process improvement and acute problem solving, ranging from production efficiency to quality improvement and delivery performance.
- We develop a digital performance management dashboard (custom or standard) including an app.
- We take on the role of ad-interim plant manager, operations manager, quality manager, production manager, supply manager, production department manager.