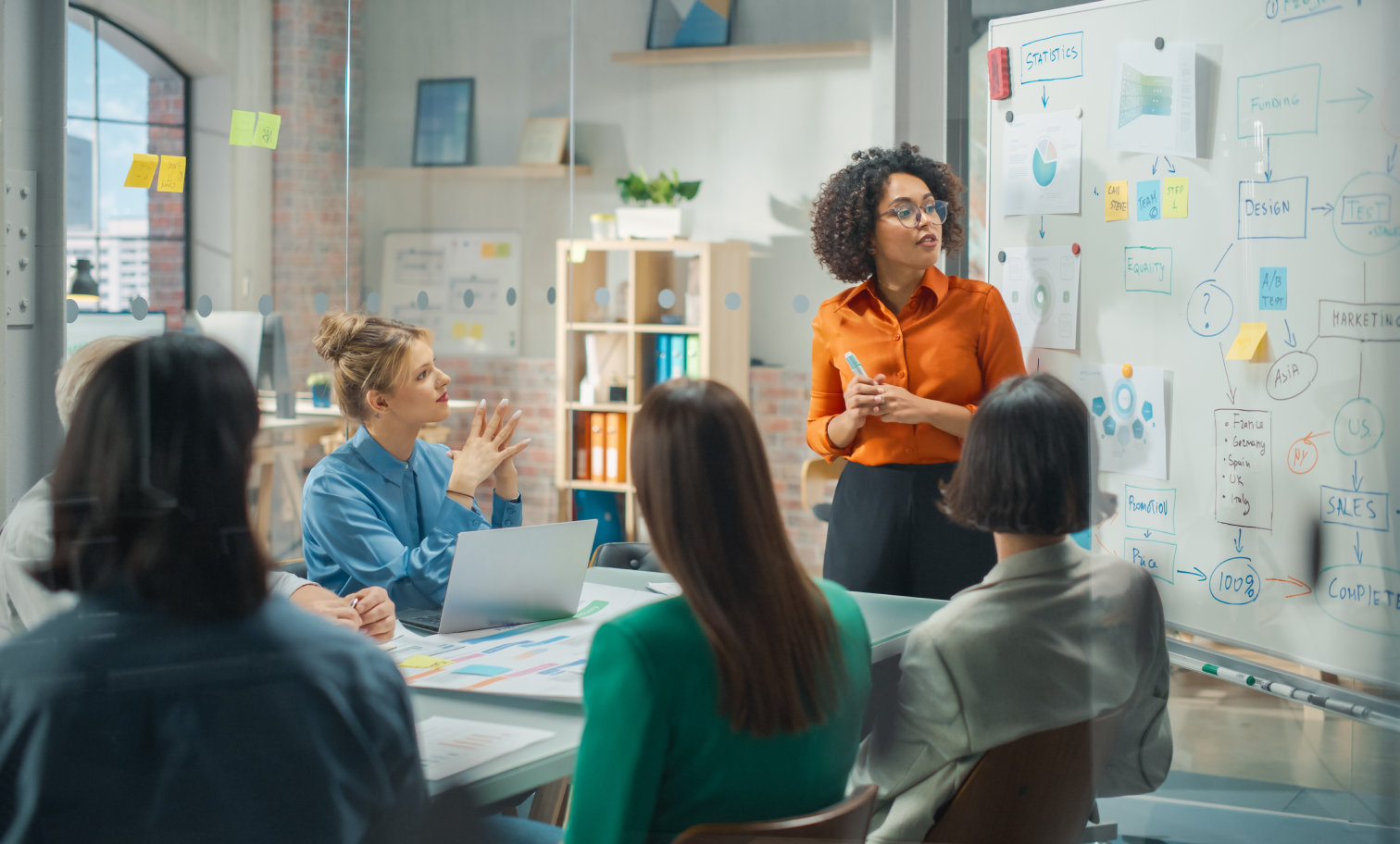
Six Sigma
Six Sigma is a problem-solving methodology which helps to eliminate defects and reduce variation in processes. This way substantial cost savings, quality improvements and improved customer satisfaction can be achieved. The DMAIC (Define-Measure-Analyse-Improve and Control) approach is used, which provides concrete tools in each of the steps to solve product and process problems based on a ‘measuring is knowing’ philosophy.
Process problems e.g. quality, production or waste problems need to be tackled in a systematic way using project management principles.
The “Define” phase covers following topics:
- Project charter with a clear definition of the problem, composition of the team and identification of the stakeholders
- Process mapping e.g. value stream mapping, process flow diagrams, SIPOC (supplier - input – process - output – customer)
- Investigation of internal and/or external customer requirements (voice of the customer) to quantify the quality specifications (CTQ: critical to quality)
- Definition of project goals
In the “Measure” phase the size and current state of the problem are mapped.
- Checking if the measurement system is adequate for correct measurements (Gage r&R)
- Identification of the most influencing factors through funnelling
- Fact driven funnelling: IS-IS NOT, pivot tables, data analytics
- Opinion driven funnelling: priority matrix, FMEA (Failure Mode and Effect Analysis)
- Collection of additional data about influencing factors
- Visualization of current state of the problem by e.g. pareto and time series plots, process control charts and process capability indices
In the “Analyse” phase the influencing factors are further explored to find the real root cause(s).
- Production, quality related problems root cause analysis tools are used
- Time or waste related problems typically lean tools are applied
In the “improve” phase potential solutions for the root causes are developed.
- Development possible solutions e.g. using brainstorming
- Selection of best solution(s) using decision matrix based on cost, impact, risk and/or other relevant criteria
- Implementation of the best solution(s) based on a detailed implementation plan using a stepwise “pilot” approach
- Start of monitoring the effect of the solution
In the final “control” phase of the DMAIC approach, the solutions are secured in the organisational systems to make sure one does not fall back into old habits.
- Writing instructions and good documentation
- Training of the involved employees
- Monitoring results (statistical process control)
- Development of Process control plan and/or Quality control plan
After the “control” phase, the project is finished. It is of utmost importance to reflect on the way of working, to keep “lessons learned” for future projects.