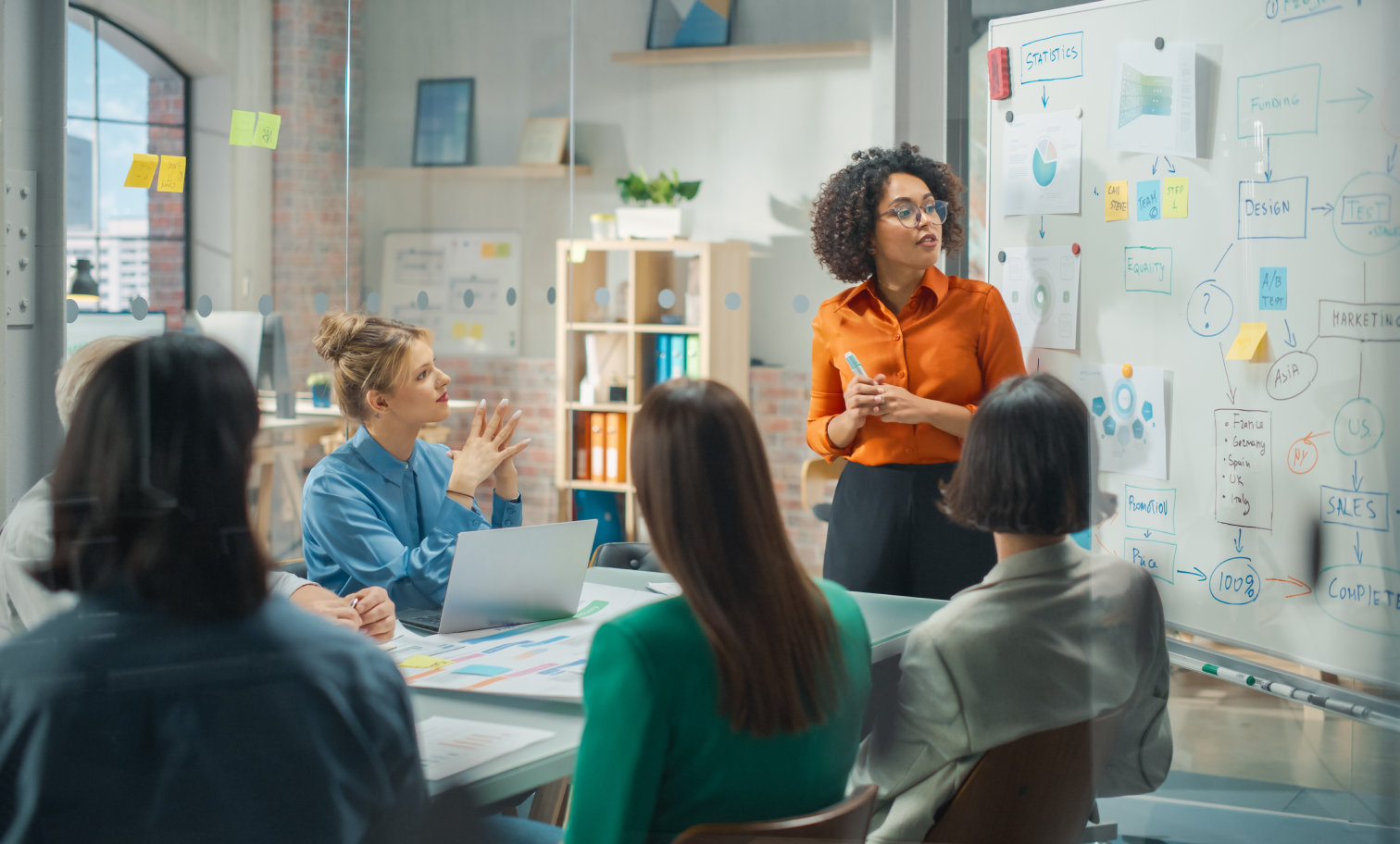
Total Productive Maintenance
Do you want to prevent unscheduled downtime of your machine park? A periodic preventive maintenance plan is needed. For this purpose ,TPM (Total Productive Maintenance) is the ideal method for: no more unplanned downtime, no more product deviations more, no more safety incidents.
TPM brings maintenance to the forefront as a necessary, vital part of the business. Production & maintenance are closing a partnership. The preventive and routine maintenance is the responsibility of the people who are on the machine every day, making firefighting a thing of the past. This frees time for the maintenance technicians to focus on root cause analysis, optimization & innovation of the machine park.
TPM creates a more efficient workplace organization that increases safety, quality, productivity & involvement!
Successfully implement TPM via the following levers:
- Measuring & increasing the OEE (Overall Equipment Effectiveness)
- Based on this measurement, the right & most important causes of non-production are addressed
- Eliminate firefighting (reactive or malfunction maintenance) by entering an effective, structured preventive and predictive maintenance system.
- Active management of machines / processes, with maintenance-free machines / processes als ultimate goal
- aimed at extending the life of the machines
- through asset reliability management (FMEA), including reliability engineering
- via condition monitoring and predictive data analysis
- through spare part (stock) management, supplier management, cost & budget management, energy management
- Expansion of a more effective and efficient maintenance team
- through skill & competence management, active use of root cause analysis, standard work, workplace organization
- Entering autonomous maintenance
- Strive for perfection - improve continuously - do not work harder, but smarter!