How R&D labs are streamlining their processes thanks to operational excellence
R&D investments only pay off when the product reaches the market. So it is important to speed up time-to-market and reduce costs. With that, we immediately touch on an important factor within Lean management: effectiveness. Let us examine this in the context of R&D laboratories.
Lean, the mindset to success
We start at the beginning: why is Lean management important? Lean is a mindset and methodology that seeks continuous workflow improvement, adding value at every step. In R&D departments and labs, value is created both during the manual processing of samples and during the capturing of associated scientific data. 'Lean process improvement' helps improve both value streams.
#1 Streamlining operations in the lab
Laboratory work requires quite a bit of manual handling. Think of sampling, microbiological research within the food industry or the crucial clinical trials in healthcare and pharmaceuticals.
Practice shows that in a lab there are all kinds of time-consuming steps that Lean techniques allow you to avoid perfectly. Based on 5S - a Lean method - which seeks efficiency in the workplace - we dotting the i's and crossing the t's on the labbench.
In addition, we follow the sample flow in a spaghetti diagram to make it as efficient as possible, and we systematically reduce “waste” by avoiding unnecessary steps. Having exactly the right lab material on hand and not storing unused samples in freezers are just a few examples. Every time we are surprised how much time this saves!
#2 Visualising digital processes
In research, value is created through the generation of data, which is the biggest difference from traditional manufacturing processes. After all, data cannot be seen, which often makes process improvement a challenge. Yet Lean can also contribute to improvements in data generation processes. The most important thing in this case is to make the invisible visible and tangible.
Although data plays a crucial role in gaining scientific insights, over time there is a risk of creating an ‘overload’ of stored data. Unstructured or unclear data management, quickly leads to inefficiencies in the form of, for example, overlapping experiments or redundant lab activities. By drawing out the process of data creation and providing structure, you solve a lot of pain points. Making the process visible brings clarity: for the scientists and lab technicians, it is clearer where in the process there are interactions and what is the next step in the data process. After all, nothing is more frustrating for a team member than waiting for someone's input. Each link feeds the next in the chain. By optimising each step, we create an efficient workflow, with a faster turnaround time as the ultimate result.
Lean management results in a clear win-win, but how do you go about it concretely? As consultants, we are happy to share our knowledge and expertise to guide you. We act as those extra eyes that clearly map all improvement opportunities, so that your organisation can achieve maximum efficiency and growth.
Our motto: ‘Drive for results’
At Stanwick, we don't just give advice, we actually provide solutions. And even that is not an end point, but a starting point. Together with the customer, we work out practical process steps and guide their implementation.
Do you want to instil the Lean philosophy in your company? Discover our range of in-house training courses and workshops.
Who is Marlies De Ceuleneer?
As a management consultant for Stanwick, Marlies De Ceuleneer is driven by science and fascinated by processes. After obtaining her master's and doctorate in pharmaceutical biotechnology at Ghent University, she developed a passion not only for quality assurance, but also for process optimisations. Behind both scientific research and process improvement is a curiosity to gain insights with data, make the invisible visible, and then implement targeted improvements. So the step from science to Lean management was easy.
"Working according to Lean principles contributes to the effectiveness of data creation processes. The most important thing in this case is to make the invisible visible and tangible."
Marlies De Ceuleneer
Contact us to discuss how we can solve your challenges with our proven approach.
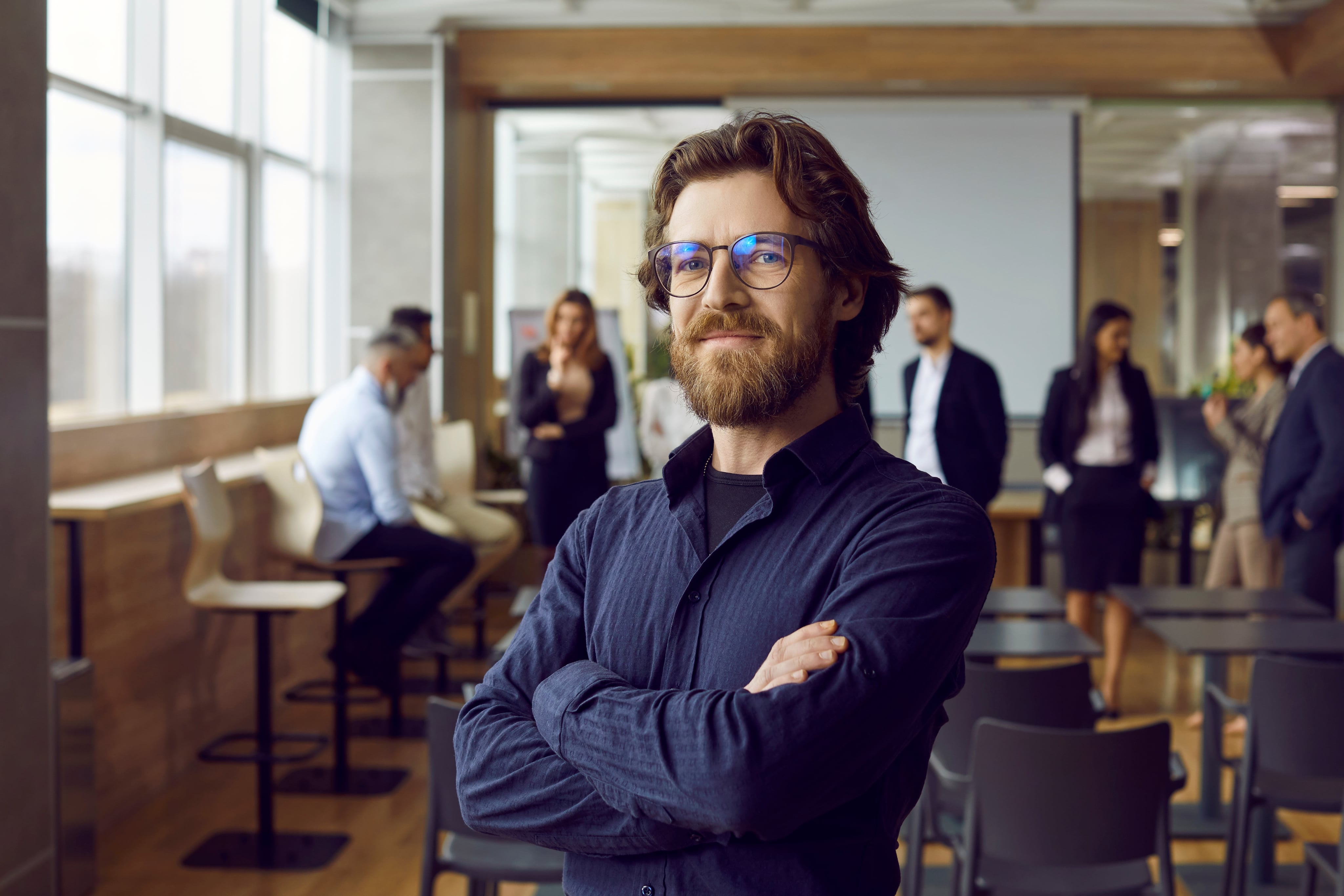
Stanwick. Drive for results
Stanwick offers result-oriented coaching programmes on operational excellence, project excellence and supply chain excellence with a focus on people, organisations and processes. We perform thorough assessments, develop clear roadmaps and implement and anchor improvements to guarantee sustainable results.
Our Stanwick Academy organises extensive training courses in which you learn together with a like-minded community about project management, continuous improvement, data-driven organisations, leadership and change management.