
Yellow Belt Lean Six Sigma
Approach
- We combine theoretical concepts with practical examples, case studies and interactive activities to enhance the learning experience.
- This training consists of 3 training days, preferably divided into 2+1.
- Participants bring their own cases. Between sessions, what is learnt can be applied to deepen the understanding of the theoretical techniques.
- In-depth cases brought by the trainers are discussed in small working groups.
- The training offers the opportunity to exchange experiences with other participants.
- The learning experience is supported and enhanced by an online learning platform.
- A training certificate can be provided.
What can you expect?
- During this three-day course, we will immerse you in the philosophy and fundamentals of Lean and Six Sigma. The DMAIC (Define, Measure, Analyse, Improve, Control) roadmap is our guide in learning and using the non-statistical basic techniques from both approaches.
- We complement this package with some of the necessary facilitation tools such as teamwork and meeting & decision-making techniques in order to implement these process improvements in a group setting. This Yellow Belt is the ideal preparation for participants who later want to delve into the more specialised approaches such as Lean Office (Lean approach specifically for administrative processes), Lean Manufacturing (Lean approach specifically for manufacturing processes), Six Sigma (focus on statistical techniques), ...
- Participants will be trained on the basic steps of a DMAIC project and the basic tools in this structure. After the training, they will be able to function as team members in project teams of the already trained Green Belts. They will also be able to take up small improvement initiatives independently.
- Intended result = after attending the training course, participants will be able to solve Non-statistical process problems autonomously according to the principles and using the techniques of the DMAIC roadmap.
Programma
- Introduction to 'Process Improvement Methodologies' and the DMAIC roadmap:
- Structured problem solving through the use of the DMAIC roadmap
DEFINE:
- Delineating your process improvement project (business case, project charter, stakeholder analysis, communication plan)
- Visualising the process (SIPOC, flow charts)
- Voice-of-the-customer (KANO, CTQs, ...)
MEASURE:
- Funnelling (priority matrix, FMEA)
- Data collection plan (TAKT time, lead time cycle time, operational definition, ...)
- Visualisation of data (histogram, pareto, time plot, box-plot, ...)
ANALYSE:
- Root cause analysis (5 WHYs, Ishikawa, 6 Ms)
- Value added - non value added analysis
IMPROVE:
- Generate, evaluate and select solutions (brainstorming, creativity, selection and decision-making techniques, implementation plan)
- Creating an efficient process: linking value added activities according to the pace and demand of the customer and application of the Lean Toolbox
CONTROL:
- Securing results: Standard Operating procedure (SOP), standardisation, control charts, documentation, training, ...
- Exploring the Lean Toolbox: including losses, flow, pull, 5 S, poka yoke, visual management, ...
We are happy to help.
3 days
Hybride (face2face - remote)
Fundamentals
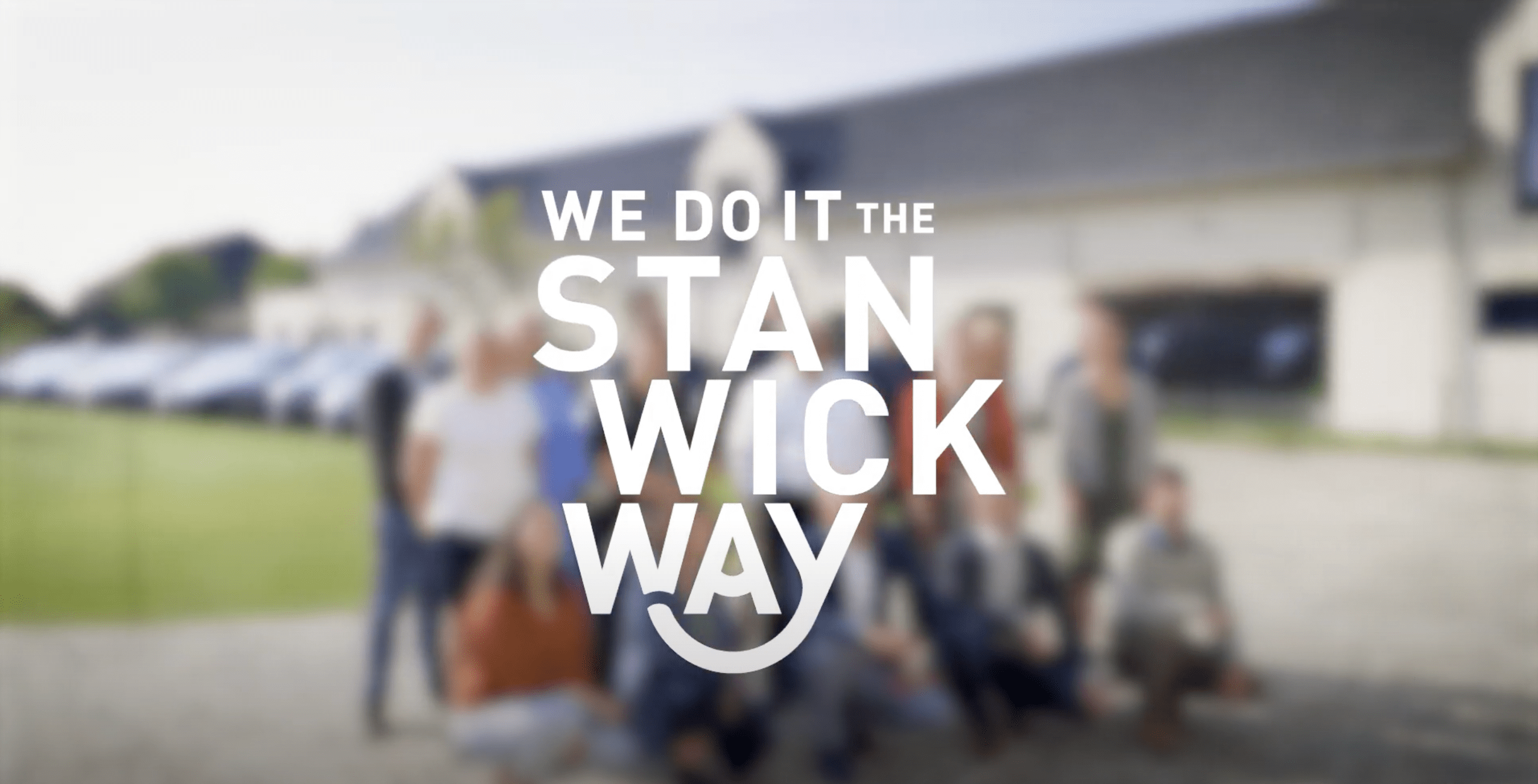
Bring knowledge to your company
Our training courses respond to the business context and specific working situation of the participants to the maximum extent. The knowledge, models and techniques introduced are immediately applicable in practice.