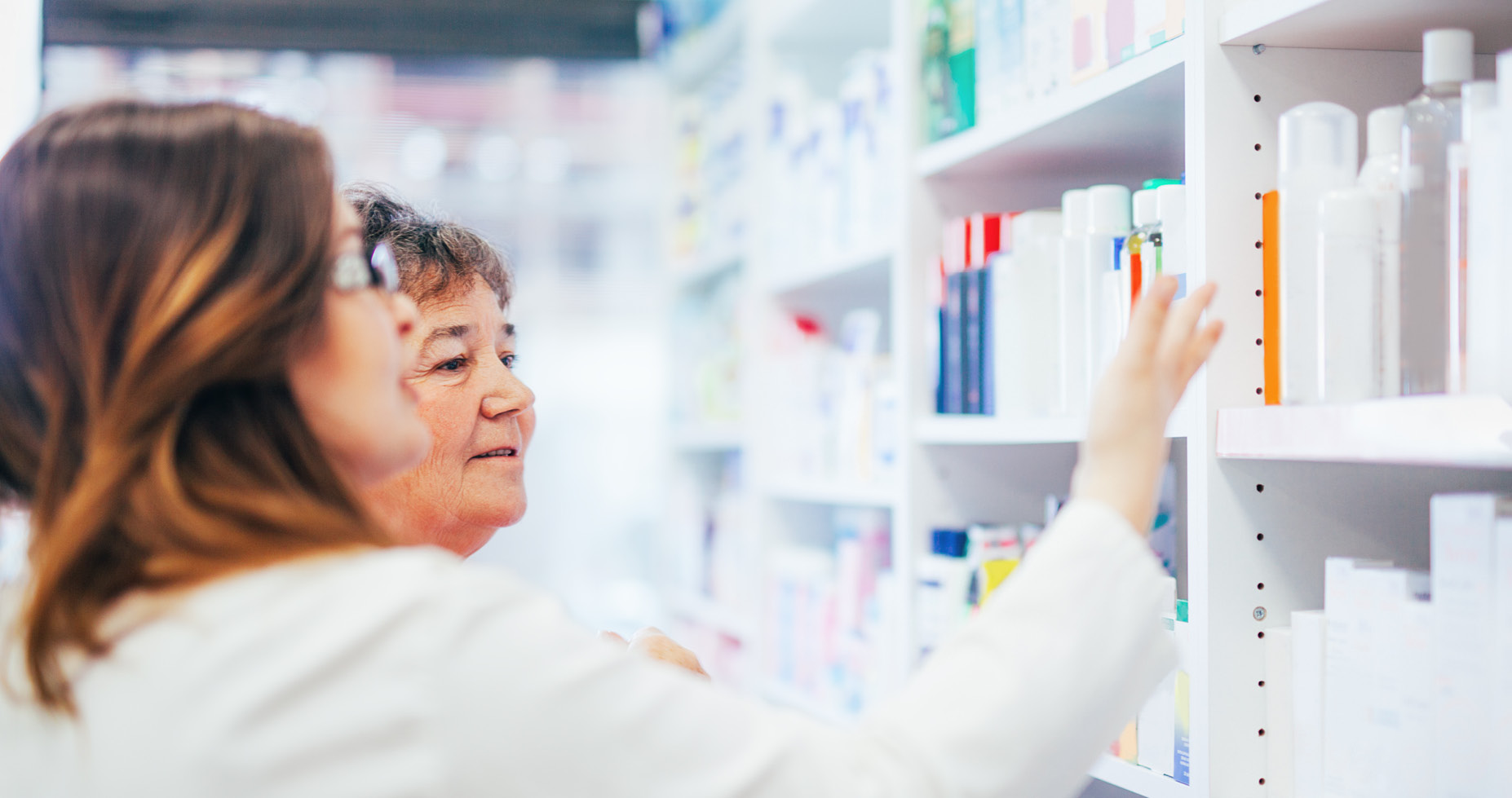
Design of Experiments
(Petro)chemicalsProject 1: Applying six sigma in the process industry
With (6 sigma) improvement projects we try to identify the most important process parameters in order to understand a process and thus to be able to steer and control it. The execution of experiments is inevitable in this respect and the Design of Experiment (DoE) approach has proven to be a very handy method.
Until recently, however, a “relatively” large number of experiments were needed, especially when many process parameters were to be studied. The invention of Definitive Screening Designs (B. Jones and Nachtheim) brings DOE within easy reach of every company, even in production environments. In the article (Chemical Engineering), we describe a comparison between a classical Response Surface Method design (RSM= typical optimisation design) and a Definitive Screening Design performed in the labs of Bayer Crop Science (formerly Monsanto). The results are astonishing. Using the DSD only 13 experiments were needed to study 6 process variables. The results of this DSD were almost identical to the results of the 90 experiments requested by the classical RSM.
With the Definitive Screening Designs, we have already achieved good results in the textile, pharmaceutical, biochemistry and metal industries, both in the laboratory and in the production environment. The DSD approach will accelerate the 6 sigma approach.
Project team: Bart Peeters (Bayer), Marc Roels (Bayer), Sam Van Aeken (Bayer) & Guido Desmarets (Stanwick)
Read the full article here: link
Project 2: Applying six sigma in the process industry
The aim of our six sigma project was to increase the capacity of one process step. To do this, we first needed to increase the stability and predictability of a key process parameter and then, in a second step, improve the stability of a quality parameter of the final product. Using the six sigma DMAIC approach and tools, the process parameter was controlled which allowed us to perform a full factorial Design of Experiment in production so that the right conditions were found for controlling the final quality parameter. The "capability" analysis shows that in about 9 months, we evolved from an unstable process with "capability" PpK= 0.9 to a stable process at "6 sigma" level (Ppk = 1.67 is even more than 6 sigma) where we no longer have outages. With the six sigma approach, we achieved our goal of significantly increasing the capacity of the process step in question, which brought us quality and productivity improvements as well as cost savings.
Opportunities have also been created for additional optimisations in the other process steps, which were not possible before and which will be investigated further with 6 sigma.