
Lean Logistics
Approach
- The Lean logistics course consists of 1 working session of 2 consecutive days.
- Each working session offers a mix of theoretical foundations and practical exercises.
- Each participant should preferably have a process improvement project.
- Feedback moments regarding progress and potential problems in these projects will be provided during the training programme.
- Each working session provides an opportunity to exchange experiences with other participants.
- At the end of the training programme, an exam is provided which, if a score of 70% is achieved, entitles you to a Lean logistics training certificate.
What can you expect?
- We provide insights into the lean tools that have proved to be a great help in solving everyday problems in an industrial environment.
- Concrete ways to apply the Lean toolbox in a structured and logical way in your own organisation (avoid cherry picking).
- Lean Logistics, a methodology developed by Stanwick, optimises these logistics processes so that they require the absolute minimum of resources to meet customer expectations. The Lean Logistics approach ensures increased output, improved information and knowledge flow, higher customer satisfaction and reduced errors, making processes more effective and efficient.
- As with any lean initiative, staff engagement is crucial but difficult at the same time. However, if you do this successfully, results become achievable and a foundation is laid for continuous improvements, as employees will be committed to new ways of thinking and working!
Programme
Module 1: Introduction to Lean Management
- The 5 lean basic principles & types of losses ("wastes") applied in logistics
Module 2: Value Stream Analysis and Process Mapping
- Techniques for value stream analysis, process maps (spaghetti diagram etc.), elimination of bottlenecks applied to process steps: Inbound, warehousing, pick/pack, outbound
Module 3: Lean Toolbox
- 5S, visual management, standard work, Kaizen, SMED, line balancing, load levelling
Module 4: Understanding customer demand & segmenting inventory
- Techniques for understanding and analysing customer needs and demands (Evolution of demand pattern & understanding variability). Methods to predict customer demand and align with logistics processes. Types of stock and impact on stock levels: cycle stock, buffer stock, event stock, safety stock.
Module 5: Lean Leadership and Culture
- Developing a Lean leadership style, creating a Lean culture, team engagement
- Working with KPIs and best practice target KPI levels (obeya)
Module 6: Problem-solving and Continuous Improvement
- Ishikawa diagram, Kaizen methodology, real-life examples of Lean improvements
- Techniques for standardisation, PDCA cycle, identifying areas for improvement
Module 7: Warehouse set-up
- Principles of efficient warehouse design and management
- Applying Lean principles in warehouse design and layout (SLP= systematic layout planning)
- Techniques for space optimisation and streamlining goods movements
Module 8: Planning and controlling a warehouse organisation
- Make-to-order versus make-to-stock
- Basic statistics applied to demand patterns & impact on stock levels
Module 9: Best Practice Analyses in Logistics: Case Studies and Practice Sessions
- Understanding product portfolio analysis and ABC classification for inventory management
- Best practices and benchmarking techniques in logistics
- Using data analytics to optimise logistics processes
- Analysis of real-life case studies, practical exercises in a warehouse environment
Optional: company visit
Testimonials
We are happy to help.
2 days
Hybride (face2face - remote)
Fundamentals
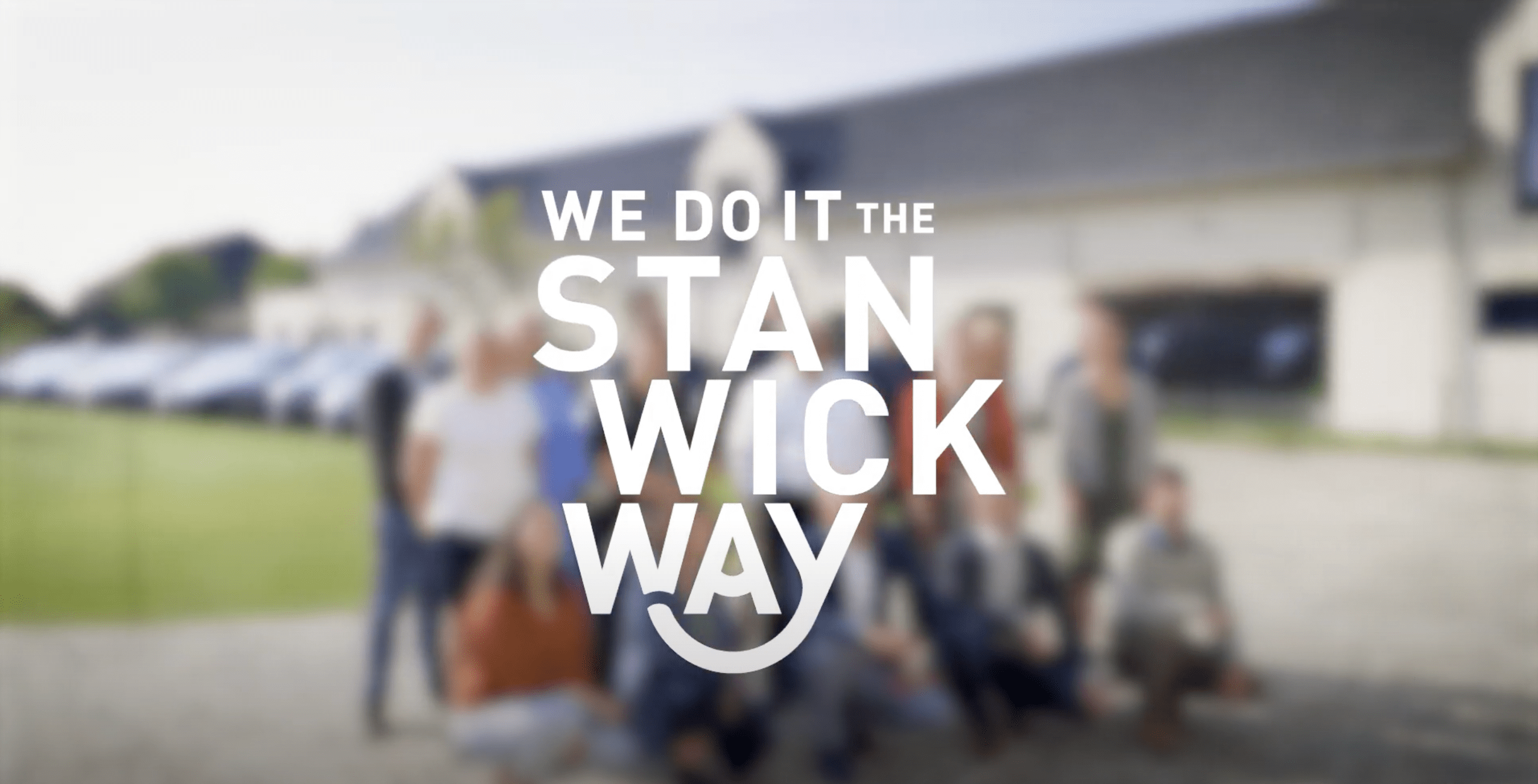
Bring knowledge to your company
Our training courses respond to the business context and specific working situation of the participants to the maximum extent. The knowledge, models and techniques introduced are immediately applicable in practice.