
Green Belt Six Sigma
Approach
- The Green Belt training process consists of 6 days or 9 days depending on the customer demand.
- Each training day offers a mix of theoretical foundation and practical exercises and offers the opportunity to exchange experiences with other participants.
- (Optional) At the end of the training program, an exam is provided that entitles the holder to a Green Belt training certificate if a score of 70% is obtained.
What can you expect?
- Analysis techniques to recognise waste in your own business processes
- Project prioritisation tools based on the differences between chronic and acute problems
- Selection criteria for choosing the right approach / tools with regard to the defined problem
- A thorough knowledge of the Lean-Six Sigma DMAIC methodology
- As a project management structure
- As a statistical toolbox
- As a problem solving toolbox
Programme
DIAGNOSE
- Basic philosophy of Six Sigma DMAIC
- Identifying problems: 7 technical + 3 human wastes
- Chronic vs. Acute variation: the Kepner-Tregoe approach for acute variation
DEFINE
- Defining your process improvement project (business case, project charter)
- Select a problem
- Prove the need
- Make a project charter
- Visualising the process (SIPOC, flowcharts, engineering map, ...)
- Assemble and build your project team
- Voice-of-the-customer (KANO, CTQ’s,…)
MEASURE
- Funnelling (priority matrix, FMEA):
- IS-IS NOT
- Historical data
- Potential mechanisms
- Data collection plan (operational definitions, contextual data, ...):
- Define important inputs
- Collect relevant data
- Be sure the measurement is right
- Visualising and plotting data (histogram, pareto, time plot, box plot, ...)
ANALYSE
- Root cause analysis (5 WHYs, Ishikawa, 6 Ms):
- Explore the process
- Explore the data
- Value added - non value added analysis
- Data analysis (stratification, hypothesis testing, regression):
- Find causation
- Verify root causes
IMPROVE
- Generating, evaluating and selecting solutions (brainstorming, evaluation and selection techniques)
- Writing an implementation plan according to the PDCA principle
CONTROL
- Control charts (Statistical Process Control) and process capabilities
- Guaranteeing results: standardisation, documentation, training, ...
- Determining Six Sigma KPIs
- Closing a project: lessons learned, project evaluation, disbanding project team
Green Belt Certification
- Participants receive, after following the training and passing the exam, a Green Belt Training Certificate. If they want to receive a Green Belt Certificate, they need to successfully perform a process improvement project according to the DMAICroadmap.
- Stanwick can coach them during this project execution and after participating in the final presentation of the project hand them their Green Belt Certificate. Please do not hesitate to contact us if you want to receive more information on project certification.
Testimonials
Video
We are happy to help.
3 x 3 days
Hybride (face2face - remote)
Fundamentals
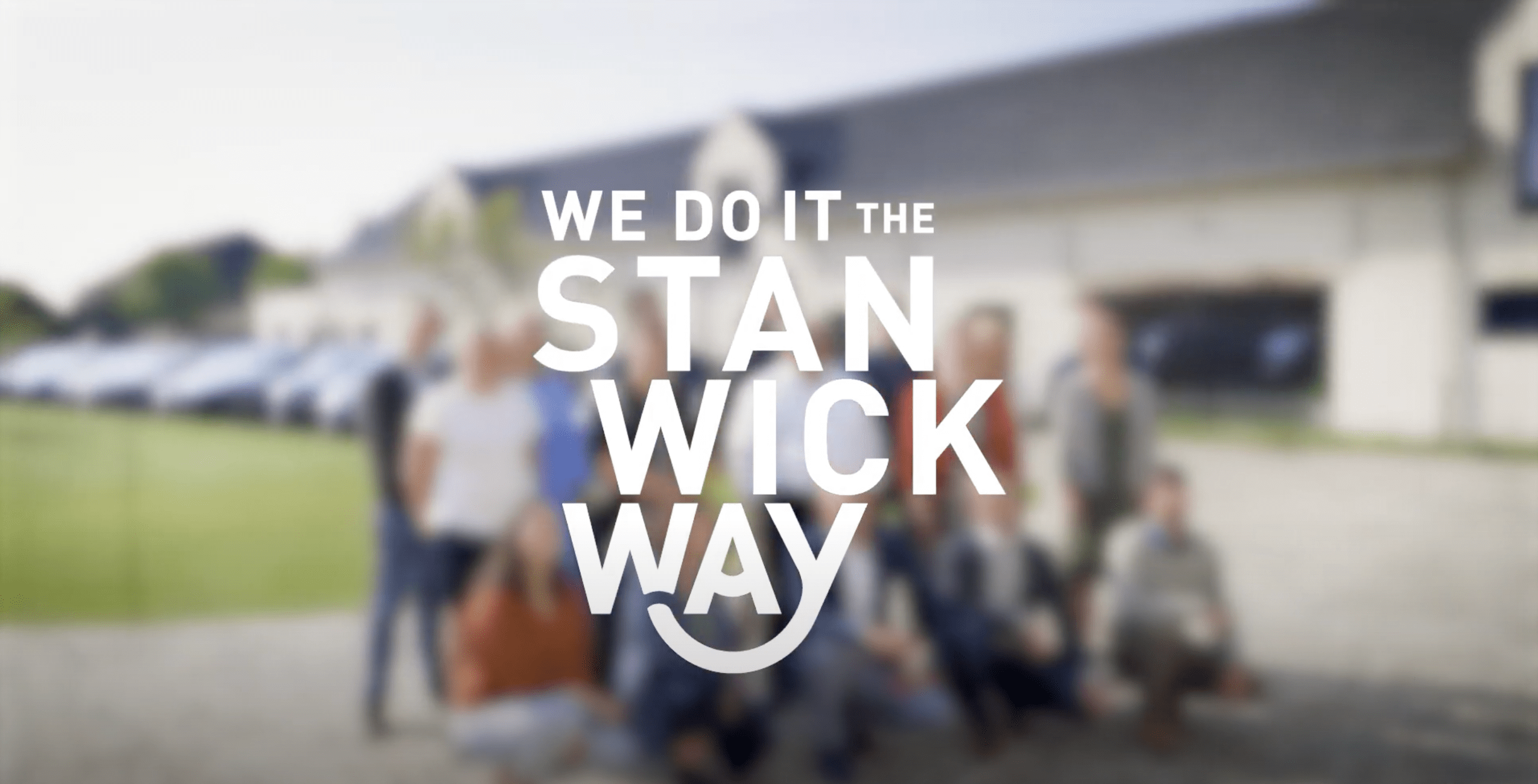
Bring knowledge to your company
Our training courses respond to the business context and specific working situation of the participants to the maximum extent. The knowledge, models and techniques introduced are immediately applicable in practice.