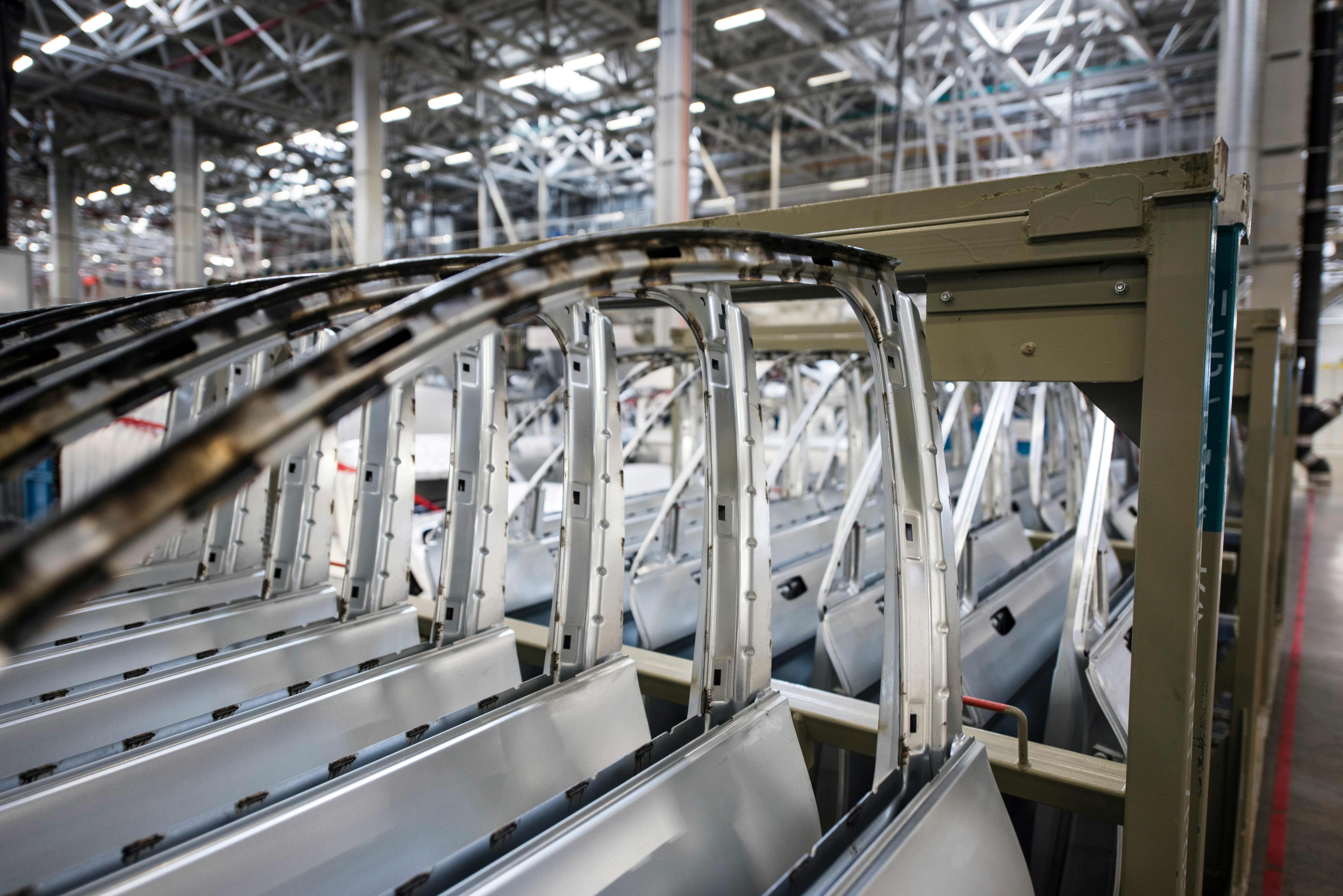
1. Culture eats strategy for breakfast:
- Introducing O.E.E. as a KPI requires maximum attention to change management. Ensure involvement and embedding in all levels of the organisation so that a continuous improvement culture can be built. This will serve as the backbone to accelerate O.E.E. sustainably.
2. Establish accurate data collection and analysis:
- O.E.E. needs different dimensions and thus different data sources. Both data of quality (rework, scrap) and availability (changeover times, breakdowns). Not all organisations have sophisticated measurement systems (e.g. MES). Do not let this be an obstacle to still start and move towards full-fledged O.E.E. measurement with small steps (marginal gains).
3. Set and measure clear performance targets:
- An O.E.E. KPI without a target is meaningless. Therefore, quickly determine with the organisation where you want to set the bar and why (see also the topic "does good O.E.E. scoring exist"). Keep measuring the O.E.E. also after implementing improvement actions. Being able to run at a higher speed on a line has an impact on O.E.E. and we also want to immediately integrate it into the visualisation.
4. Train and involve team members in the process:
- O.E.E. is not a KPI of 1 individual or even 1 department, no it is a cross-departmental KPI that therefore requires that practical knowledge around O.E.E. improvement is also embedded in the manufacturing company. From the start of an O.E.E. transformation project, it is therefore crucial that you have mobilised a core team and that they not only acquire knowledge on O.E.E. but also on how to improve it project-wise through Green Belt improvement projects (more info on Green Belt, see link).
5. Keep the overview and make a roadmap for the plant or multi-site organisation:
- An organisation simply has limited resources. Stanwick is therefore often involved to perform an O.E.E. assessment to determine what the first improvement projects will be on which machine in which factory. For strategic, financial & operational reasons, a certain improvement project may still be given high priority. A project portfolio governance structure brings direction and focus. By focusing on 1 line, a lot of attention goes to that line (e.g. maintenance), which could cause you to neglect other lines. It makes no sense to improve 1 line in the factory and let all the rest go down. Don't lose the overall picture.
What is the role of a Stanwick consultant in O.E.E. improvements?
From Stanwick, we have 3 possible roles that we include in operational excellence processes where we improve Overall Equipment Effectiveness (O.E.E.):
- Stanwick trainer
- Stanwick consultant
- Stanwick interim project manager
Learn more about the 3 roles: https://www.stanwick.be/en/about-stanwick
What are the Stanwick cases in Operational Excellence trajectories?
From Stanwick, we have supported several O.E.E. transformation projects in numerous sectors (chemical, pharmaceutical, petrochemical, food, construction industry).
Learn more about our cases: https://www.stanwick.be/en/cases
Feel free to contact us for more info.
Jeroen Van den Hove
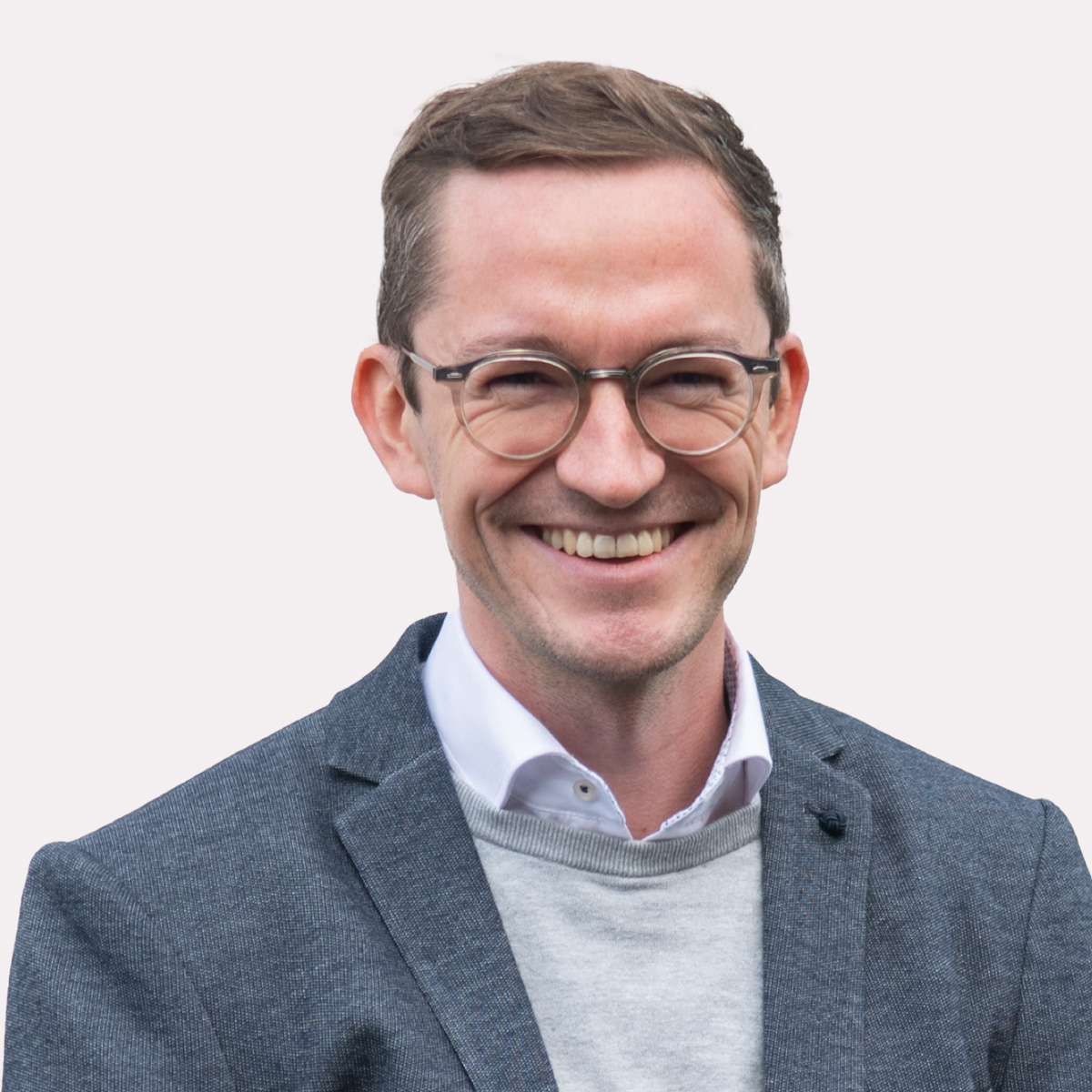
Jeroen Van den Hove
Operational Excellence – Lean Supply Chain – Portfolio Management
jeroen.vandenhove@stanwick.be
Process improvement
Today we are flooded with tools & techniques to improve our business process. Just think of Six Sigma, TPM (Total Productive Maintenance), Lean, QRM (Quick Response Manufacturing), TQM (Total Quality Management), ... All these techniques have undeniably their advantage, but are often built from a well-defined vision. An integrated approach is thus required.
English